Rail grinding: how SkyTrain ensures your commute is safe and comfortable
Rail grinding: how SkyTrain ensures your commute is safe and comfortable
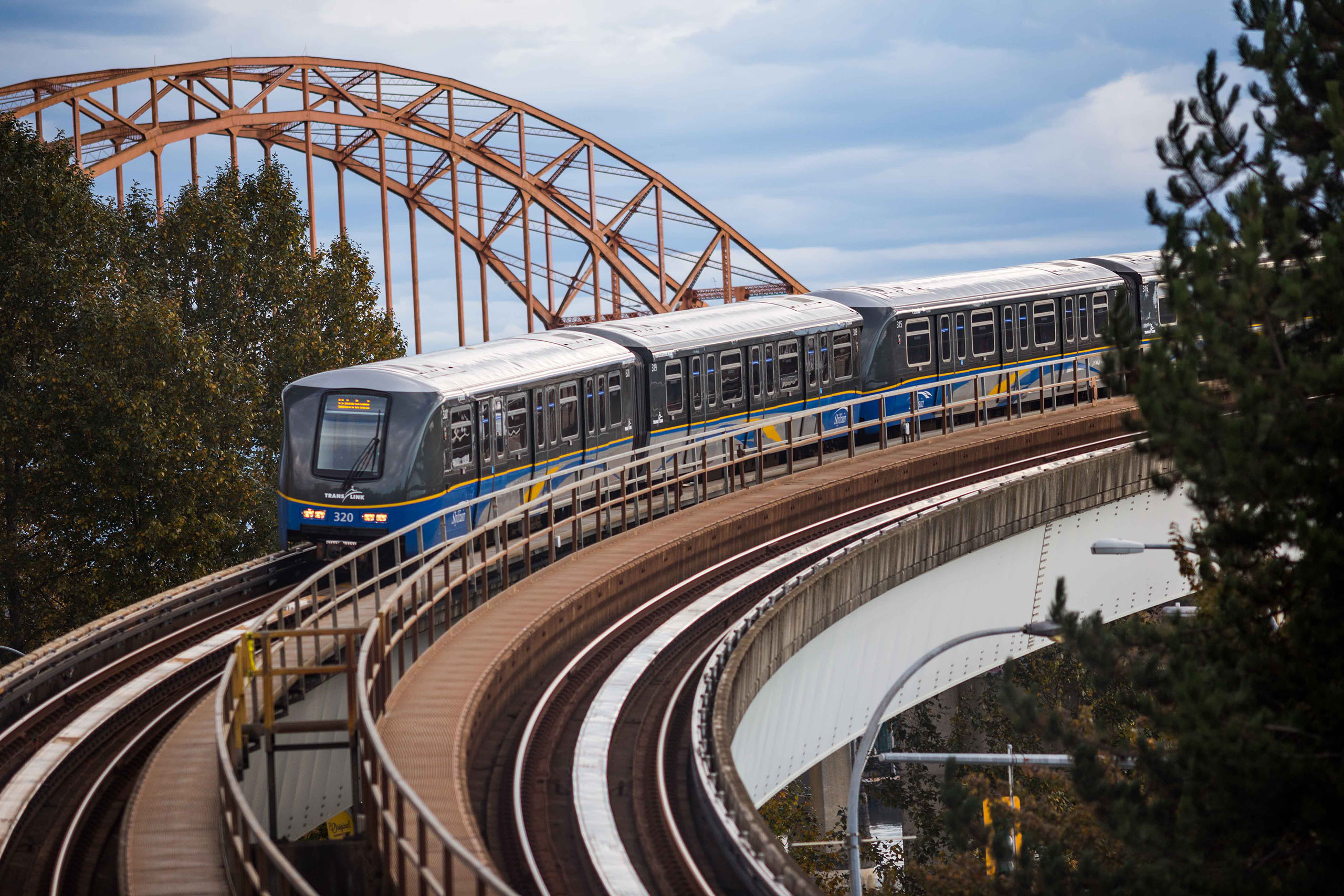
Our SkyTrain rails go through a lot every day. With trains running for 20 hours daily, they’re constantly under stress. Vibration, impacts, and wear and tear from train traffic have a huge cumulative impact on the tracks that take you where you need to go. This stress doesn’t pose a danger to our passengers or trains. But where and tear can lead to bumpier and noisier rides leading to a less comfortable or slower commute.
The good news is that we reduce the impacts of regular use through carefully managed rail grinding maintenance. Rail grinding is a process in which both British Columbia Rapid Transit Company (BCRTC) employees and outside contractors grind down the metal of the SkyTrain rails. They do this by using specialized machines to smooth the contact surface that the trains ride on. The efforts to smooth rails and maintain passenger comfort is how we keep our system in a State of Good Repair, which is one of TransLink’s driving philosophies.
Our system’s success is built on maintaining the old and investing in the new. If infrastructure maintenance and upgrades are your jam, make sure to stop by the TransLink website to check out past, present, and future projects in TransLink’s Maintenance and Upgrade Program.
How it works
The grinding process is done mostly by SkyTrain Guideway staff who utilize the aptly named “Rotary Grinder #1”. These contracted grinders are large, high-powered machines that allow workers to accomplish more maintenance during our brief closures each night. The LORAM machine, which is about the size of a SkyTrain car itself and rides along the rails, grinds material away making the rail smooth.
“The principle of rail grinding is to remove a thin layer (~.1mm) of the rail steel, which effectively removes defects and rail surface fatigue, as well as rail roughness such as corrugation,” explains Peeter Vesik. Peeter is a former Technical Analyst with
While many might know why the grinder visits our system each year, few might be aware of how it achieves its goal of removing this thin layer of rail steel.
“The grinding process involves a sequence of passes, back and forth, which cover the head of the rail, removing facets of material at precise locations,” adds Peeter. It is a delicate and intricate system, as rail needs to be set within a defined target profile to achieve the best performance and maximize asset life. These are top priorities for our workplace to keep our colleagues and customers safe and secure while using transit.
Improving each year
This year, the LORAM grinder completed more grinding on our system than ever before, touching on almost two-thirds of our system. This is a significant milestone in our State of Good Repair program and demonstrates the cumulative steps we have taken at BCRTC to prioritize maintenance work in the past five years in particular. “In 2021, the contracted LORAM yielded 75.9km of completed track in 40 budgeted shifts, the most LORAM has ground in one annual program at BCRTC.”
“In each year since 2018, the contracted grinder has incrementally increased the amount of completed track meters per shift. For us in rail maintenance we see this as a systemic condition improvement, increasing by small amounts in the right direction each year,” Peeter reports happily, having seen the progress of the work and investment done to improve our rail.
You could be forgiven for mistaking that extra kilometers of rail ground equates to a worse system state, or “more work required”. At first glance, it might appear that if we must grind more areas, that means we are experiencing more rail defects. However, as Peeter is quick to point out, quite the opposite is true.
“A segment of track that is in preventative state will likely see between seven to nine passes, whereas track that requires significantly more restoration can exceed 20 passes, or approximately twice the amount of time to complete a meter of track. If we are in better condition as a system, we will be able to spend less time on a single area and cover a larger length of track as a result. When we start seeing areas being brought into specification in fewer passes, thus we have opportunity to grind more elsewhere for the same budget, this is an indicator that not only is the rail health improving, but we are heading towards a preventative state, the goal of all railways.”
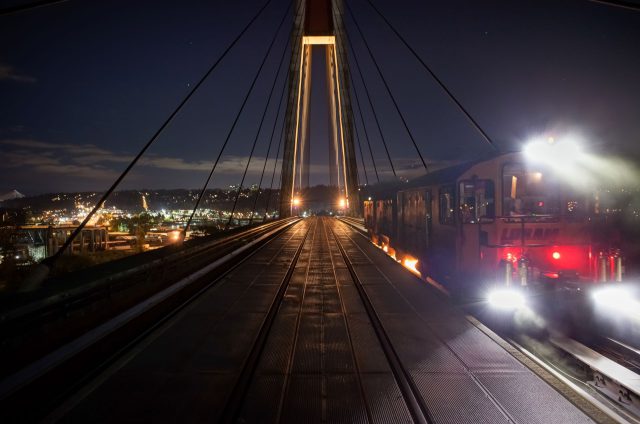
Another reason the contracted LORAM grinder was able to do so much work this year is due to the substantial work of our in-house grinder which completed about 60 kilometres of track. The in-house grinder also can grind switches and stations, something the LORAM can’t do. The two grinder systems work in tandem to be able to offer safe and reliable service throughout the SkyTrain network year-round and without causing any delays to service.
Peeter, the hardworking maintenance staff at BCRTC, and the contractors who operate the LORAM are just some of TransLink’s valued staff that keep you moving to the people and places that matter most.
If you have any questions or concerns let us know below. Alternatively, if you have any requests for more information or stories about how we keep you moving, leave a comment or send us an email at thebuzzer@translink.ca.
What did you think of this story?
Don’t you think, Skytrains are riskful and these can make some serious situation during emergency.
In my opinion I think this is not good for anything.
It happens a numerous times since the Expo line is 36 years old, the Millennium Line is expected to be 20 years old soon as it is and the Canada Line is 12 years old and TransLink, BCRTC and ProTrans BC are taking things seriously within serious situations during emergency, It appears your opinions about it makes you stressed out. So the SkyBridge’s Track replacement is now over and please don’t take it seriously with your anxiety. All BCRTC/ProTrans BC’s Track Maintenance Workers uses safety whether it’s a Track Maintenance or Track Replacement when the track gets older and older, it sure needs a new one. Just let it go man and some of the workers worked out safely without incidents. :) Besides Capstan Station is now doing it’s Infill using one platform at a time and the right side next as well. There’s also a Canada Line single lane travel that is happening now until February 2nd. Can you calm down? I’m just asking and I know some people has negative thoughts as a opinion. Chill in and please have a lovely day!
The rail system is very modern and safe.