TransLink Podcast: What’s the T on why SkyTrain doesn’t run 24 hours
TransLink Podcast: What’s the T on why SkyTrain doesn’t run 24 hours
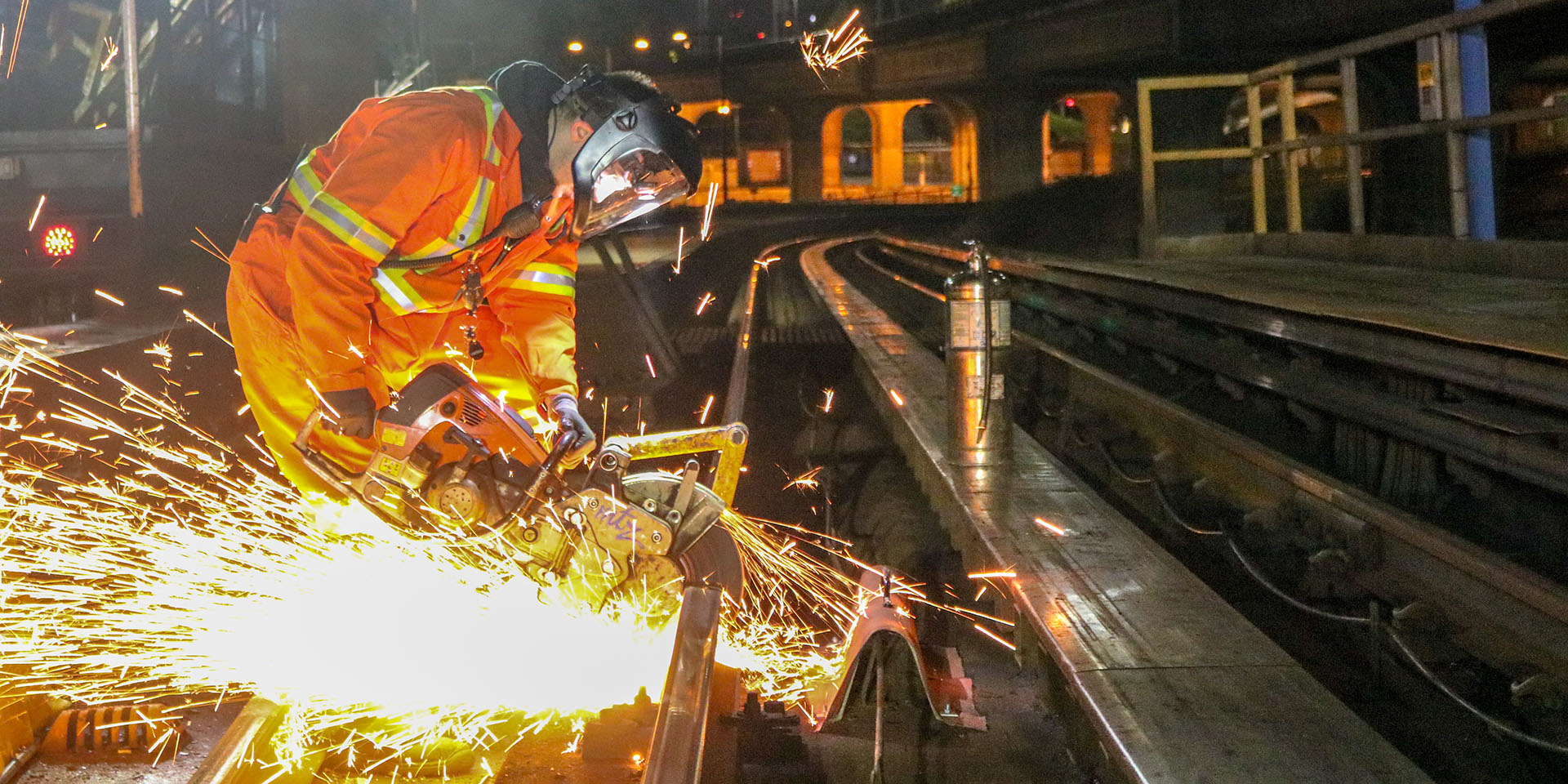
Matt Doyle, SkyTrain’s vice-president of maintenance and engineering, has the answer why the SkyTrain doesn’t run all night. He also explains what’s going on behind the scenes on the SkyTrain tracks overnight when most of us are asleep.
Transcript
HOST JAWN JANG: Hey, welcome to What’s the T. I’m Jawn Jang. I’ll be your host as we try and tackle one of the biggest questions that you, the public, have asked about the SkyTrain for nearly four decades. Why doesn’t the SkyTrain run all night?
CUSTOMER 1: If I had to make a guess, I just. Because maybe not enough people use it.
JAWN: It’s a good question. So, do we have a good answer? Let’s tap in to What’s the T.
[INTRODUCTION MUSIC PLAYS]
VOICEOVER 1: The next station is.
VOICEOVER 2: Welcome to What’s the T: the TransLink Podcast.
JAWN: TransLink is the regional transportation authority for Metro Vancouver and that means you see us at work every single day. From the SeaBus and West Coast Express to the many different busses on our roads to perhaps the most iconic public transportation medium in our region, the SkyTrain. With over 300 train cars in service, BCRTC — or the British Columbia Rapid Transit Company — has a crucial role to play in transporting the thousands of people who depend on their service every single day.
And since the Skytrain launched in 1985, it has become an icon as a completely automated and fully electric rail system. But, in the nearly four decades, the Skytrain has dutifully served the residents of Metro Vancouver, it has faced one very specific question that people still ask to this day. Why doesn’t the SkyTrain run 24 hours?
[AN EXCERPT FROM SEMISONIC’S “CLOSING TIME” PLAYS]
JAWN: Now, before we hear from the experts, what do you think? Why does the SkyTrain have a daily service window instead of just running all day and all night? You’ve probably come up with a theory or two in the past. We tasked our very own Thor Diakow out to hit the streets and hear directly from customers like you. And here’s what you had to say.
INTERVIEWER THOR DIAKOW: Hey, its Thor with TransLink, we’re here on the system asking people why they think Skytrain doesn’t run 24 hours a day. Do you have a theory on why SkyTrain doesn’t run all night?
CUSTOMER 2: I actually didn’t know that, honestly. I mean, maybe not enough users at night because I don’t use it at night, that’s for sure.
THOR: Why doesn’t the SkyTrain run all night?
CUSTOMER 3: Well they have to do some maintenance some time.
CUSTOMER 4: There’s not enough ridership to justify it. That’s what I would expect. Yeah.
THOR: We’re asking people why they think SkyTrain doesn’t run 24 hours a day. There’s a lot of different ideas around that. But why do you think it doesn’t run all night?
CUSTOMER 5: If I had to make a guess, I just ’cause maybe not enough people use it.
CUSTOMER 6: No, no idea. I’m not sure.
JAWN: Okay. A lot of different answers. Some pretty solid theories in there. But are any of them correct? In order to solve one of Metro Vancouver’s oldest transit mysteries, let’s go directly to the expert who can finally crack the riddle.
GUEST MATT DOYLE: I appreciate the question, and I’ve had some experience answering this question historically.
JAWN: Matt Doyle is the vice president of maintenance and engineering for BCRTC. Take it away, Matt.
MATT: Yeah, the reality IS, it’s as simple as we require time to do maintenance. It’s the simple answer to a complex question. But in order to operate our trains and our tracks safely for our traveling public, we need that downtime to basically get into both THE trains, the rolling stock, as well as into the track and guideway areas, as well as all of the supporting systems and networks in order to keep, you know, high reliability, safe operation for our operating window.
JAWN: So if you’ve guessed maintenance, then give yourself a pat on the back. Very well done. Maybe you should be working for us. But what does that actually mean? What does maintenance look like every night and why does it need to happen during those overnight hours?
MATT: Yeah, we tend to use that in-between as non-revenue windows. So quite simply, the time when we’re not running revenue service. So that non-revenue window is basically, yeah, when we have safe access to the system. It can be accessed multiple ways. So we’ll kind of give a couple different scenarios for the listeners to understand. Primarily if we’re doing any type of repair work, or any type of, we refer to as a linear, visual inspection, we use special equipment.
So we have rail borne equipment. Little speeders and crane carts and other things, including rail grinders that run on our system. And they actually operate on the exact same tracks that the revenue service operates on. We cannot have revenue service operating at the same time due to safety and quite honestly, chance of collision, etc. So that equipment, because the nature of our guideway, needs to be launched from an area, so it tends to be launched from one of our operations and maintenance centres, you know, as the last revenue train is running, we start to fill in behind that revenue train to launch our equipment, get folks to the job site for that evening or morning, I should say. Usually around, you know, 1 a.m. in the morning through till, you know, four or five depending on the day and gets crew, equipment, tools to site to either inspect, repair, maintain or replace — you know the job for that day.
JAWN: So it sounds like your team obviously does a lot in those overnight hours. I’m wondering, is that even enough time? Like, does your team have enough time every night to take care of everything they have to do? Or would you ideally kind of want even a little bit more time to take care of everything?
MATT: Yeah, you’re going to get me in trouble here. But yeah, if we shut down the railway all the time, then I can keep maintenance going on, you know, the extreme. So we’ve been pretty strategic in how we do that. So we basically staff up, we, we have equipment that that gets us to site and basically we design our maintenance regime around that kind of the available non-revenue window.
There are times and we try not to lean on this too much, but there are times where we do need to actually offer an alternative service. So people who ride the system in the evening will notice for some years now we’ve been running an alternative service at different areas of the system to support some major rail replacement exercises.
What this means is, we use the term a single track and we basically run the revenue service around a section of our system, and that gives the maintenance crews and other major works crews access to that area of track for a longer window. So again, for the one that’s the most probably most prevalent for the listeners is our evening single tracking window — Sunday nights usually through Thursday nights. We kind of start single track and I believe it’s around 2100 hours through end of service and basically gets, you know, an extra 3 hours of track access to facilitate that critical work. So we can do a lot in that non-revenue window. But there are times where we do need to, you know, further disrupt our passenger service in order to keep the system safe.
JAWN: You know, I think a lot of people can relate to what maintenance is like because we all live somewhere. We all know what it’s like cleaning the house or the apartment. It takes time. And sometimes we just dedicate like one day of the week to doing it. For me, it’s a Sunday. I’m a Sunday cleaning guy, but maybe take us into the challenge of maybe working and maintaining a system that was made all those years ago.
MATT: Yeah. So with any kind of major infrastructure works, there is, you know, your normal maintenance regime is consists of inspection, preventative maintenance. So kind of utilizing your house example, that’s when you’re doing your, your dusting, your cleaning, wash the dishes, put the dishes in the dishwasher — your day-to-day maintenance. As the you know, asset ages or as you’re your home ages, then you need to start doing more work.
You need to start replacing the roof. You need to repaint the siding. You need to do, you know, all this other type of stuff. So, we are seeing that, for a lot of our systems have reached that and actually in the last, I would say, ten years, we’ve actually replaced a lot of our systems and people may not have actually realized that.
But that’s, you know, happening under the trains that run on the rails, so the rail almost all the way from Waterfront into Scott Road has been replaced, you know, or is in process of being replaced over the last ten years. We’ve replaced a lot of our turnouts.
We’ve upgraded a lot of our technology. You know, you see some of that in the stations with new screens. But in order to get those new screens, you know, there’s new cable being run. You know, we’ve upgraded from analog cable to fiber optic cable to support the transmission of the camera signals back to our control centre, be able to facilitate the communication, whether to those nice screens that the passenger information displays or to the, you know, PAs in the station.
So all that stuff is things that have been basically upgraded, you know, underneath the train, so to speak, over and over the last number of years. And unfortunately, we’ll need to continue to happen as we as we age the system. The next key kind of pieces of infrastructure is starting to replace our power system. So we get lucky enough we, you know, run on electricity, we get a lot of hydropower through BC Hydro, but that goes into substations and switching equipment that is reached end of life.
And we’ll be starting to replace that. Luckily for our traveling public, that is something that can be happened kind of behind the scenes. It doesn’t require the system shutdowns that we see, but there’s always going to be, you know, a chance that we need to increase maintenance windows to facilitate those types of operations.
JAWN: When your work is on notice, that’s actually a good thing.
MATT: I was just going to say that Jawn and I recall actually speaking at a I want to say a board or a public meeting back, you know, in early in my tenure with SkyTrain. And success for us is no one knew we were there. And it’s a little bit of a weird mantra and it’s something that, you know, it can be challenging to kind of get the recognition because ultimately the only time people know where there is when something hasn’t happened.
If we do our job, people go, you know, ask the questions, why can’t we run 24/7? They never see anybody out there and ever see anything happening. You know, that’s when I actually, you know, give my team a pat on the back saying perfect and no one knew we were there. We’re successful.
JAWN: You know, stealthily in and stealthily out. You guys are like a team of commandos basically every night, just making sure you do your job. With respect to the SkyTrain cars themselves, I don’t know how many people realize the work that goes into just making sure they’re clean. And, you know, when people get into them and sit down that it’s a pleasant experience beginning to end.
I had a chance to go down and tour your facility, and I saw what it was like to kind of see the cars from underneath and get a look inside. And clearly there’s a lot of work that goes into that as well. How long does it take on average, if you can maybe give me that number, that figure to simply clean one single Skytrain car to make sure it’s good to go?
MATT: Yeah, that’s a good question. I know that every car gets cleaned daily. So basically every vehicle goes through our vehicle cleaning and inspection facility at our two OMCs [operations and maintenace centres] and actually gets a quick clean. I want to say it’s in the order of, you know, 5 to 10 minutes per car to do a regular cleaning. Unfortunately, there are times when, you know, a deeper clean is required and that will be dealt with.
But we’re basically have a team of cleaners that descend again, you know, similar to our maintenance window where you basically staff up to match the available window. So, you know, we throw more resources at it to capture that that short window that we have. I think it’s in the order of about 5 minutes per car that we spend, you know, and then the next train comes in and, you know, it’s a kind of a ballet that happens between that between the clean lanes where people go back and forth.
And that’s just to keep the cleanliness of the cars for the public. Obviously, the trains themselves have their own maintenance regime. They’re into the shop at minimum every six weeks in order for a full inspection. And then different maintenance regimes that go through to keep them, again, safe, reliable, but also to get them to last their design life.
I think our Mark Is are close to reach an end of life. They’ll be retired soon. We’re both, you know, a little bit of regret seeing them you know go away but also excited to see new vehicles come in, new technology.
JAWN: So yeah, the Mark Is, I mean, hey, they’ve been they’ve been doing their thing for a very long time. I don’t think anyone can ever say that they didn’t live up to what they were supposed to do. Good for the Mark Is, they get to retire, at some point and keep their heads held up high. Talking about your team of commandos, Matt, like on average, do we know how many people are working on the system every night? And maybe people can get an appreciation of what kind of work that really means?
MATT: We have our own staff, so there’s probably about 120 staff that are working most evenings. That’s just the maintenance side. There’s obviously the, you know, our control room operates 24/7. So there’s the control folks that are there. But because of the nature of the investment that’s underway, both in renewing our aging assets but also looking at the expansion and growth, there’s a team of contracted staff that are that are working on the system every single evening. And the number of unique work sites can be upwards of 2 to 3 dozen different work activities underway in a single non-revenue window in order to kind of keep everything up, up and going and get us ready for that morning service.
JAWN: We now know like how big that team is and the important work they do every night. But I’m sure there’s also like daytime counterparts, you kind of do a lot of the prep work. So how big is that particular team if we have a ballpark figure for that?
MATT: Yeah. So the overall maintenance division is in the order about 400 individuals, 400 employees. And we actually do a lot of work during the day. So appreciate that this discussion has been around kind of that non-revenue window and what that avails and why we need that. But there’s actually a lot of work that happens during the day.
We can inspect we inspect some tracks during the day where we have the ability to get safe access for visual inspections. A lot of our train cars can be maintained during the day. You know, trains that aren’t in revenue service. But then, there’s teams that are involved in planning that night window.
We have planners, schedulers, safety reviews of safe work practices, you know, we’re prepping equipment, prepping materials to be prepared to be deployed. Sometimes we’re driving to a site and leaving things below and pulling things up in that non-revenue window. So, yeah, large swath of folks that are doing the work to basically to try to minimize customer impact, maximize the opportunities we have to do the maintenance required in the windows that we have in order to keep providing the safe and reliable service that we’re all very proud of.
JAWN: So, Matt, final question. What are things that people should know when it comes to maintaining the SkyTrain and the and the entire system really from top to bottom?
MATT: Yeah, I think just really would love people to see the pride that all of our employees take in the work that they do and the volume of effort that’s required to keep the system safe, keep the system reliable. And that just speaks to the professionalism, quality and just the competency of the crews that are out there every single day, 24 hours a day, seven days a week, wind, rain, snow, sun, they do it all and they do it to keep the system running. And they’re very proud of it and I’m very proud of them.
JAWN: Now, you’re probably saying, wait a minute, Jawn, there are systems that run 24/7. And you’re right, parts of the New York City subway runs 24 hours. Select lines of the London Underground provide 24 hour service on Fridays and Saturdays. The Copenhagen metro operates 24 hours a day, seven days a week. So why can’t Metro Vancouver SkyTrain simply run 24 hours?
GUEST DAVID COOPER: TransLink runs a very high frequency service in the SkyTrain. It’s a high demand piece of infrastructure.
JAWN: David Cooper is the principal at Leading Mobility Consulting. His team works with transportation agencies from all over North America, and Coop is able to provide some fascinating insights when comparing how we do things here in Metro Vancouver with other cities that do offer 24-hour service.
DAVID: The challenge for 24-hour SkyTrain is that in order to have all around the clock services, you need to have redundancy in the network. So if you look at the subway system in New York City, for instance, they have many lines that are four track. And if you go down to the subway, you’ll see very kind of complicated sign that’ll say, you know, at nighttime, you’ll take this line for this segment. You’ll take that line for that segment because they’re trying to maximize the track infrastructure and station infrastructure they have because there’s redundancy in the network there. There is very little track time available for maintenance staff to check on switches to do tactical equipmen maintenance in a very short period of time.
You know the last Skytrain leaves Waterfront Station at 1:16 in the morning and it has to run all the way down to King George and then come back to the to the operations centre at Edmonds and you really only have about 2–3 hours to do very core work to make sure you have service the next service day.
JAWN: Redundancy in this case means having extra tracks. So as an example, if you had four tracks, you could theoretically close two of them so that your maintenance crews can get in place to work while running train service on the remaining two open tracks.
That being said, the SkyTrain is a growing technology and a growing infrastructure in metro Vancouver. Consider the Broadway Subway project or the Surrey Langley SkyTrain project. For Matt and the rest of the team in maintenance and engineering, they’re up to that task.
MATT: It is exciting for us to face that challenge. It is a challenge. It is going to be a big challenge. How we kind of adapt our work processes, what new technology we can invest in, you know, how we keep staff trained and how we keep staff current and able to do that work is an exciting challenge. You know, we have two primary goals here at SkyTrain at the moment.
One is to maintain our excellent daily service and the second one is to build for the future. And those are both our number one priority. And I think that speaks to both the complexity and the excitement that we’re seeing here, is how do we continue to meet our existing customer expectations and exceed, as well as ensure that we are successful for this really exciting expansion that’s underway at the moment.
JAWN: No, the Skytrain doesn’t run 24 hours, but what it does do is connect us. It takes us to school, to work, to family dinners, sporting events, concerts, festivals, gatherings and everything else in between. Because like I said, it has become one of Metro Vancouver’s most iconic sights and sounds and one of our most reliable modes of transportation. Thanks for joining us here on What’s the T.
Don’t forget to subscribe to catch the very next episode. And hey, if you want to get in touch, you can always send us an email, podcast@translink.ca. That’s podcast@translink.ca. We accept questions, comments, concerns and even compliments. Yeah, believe it or not.
My thanks to Matt Doyle, vice president of maintenance and engineering, and Alex Jackson, senior internal communications advisor, plus the entire team at BCRTC for helping to make this episode possible.
Special thanks to our producer Allen Tung, the entire digital content team at TransLink and you for listening. I’ve been your host, John Jang. Until next time. Have a safe trip.

